RESEARCH AND DEVELOPMENT
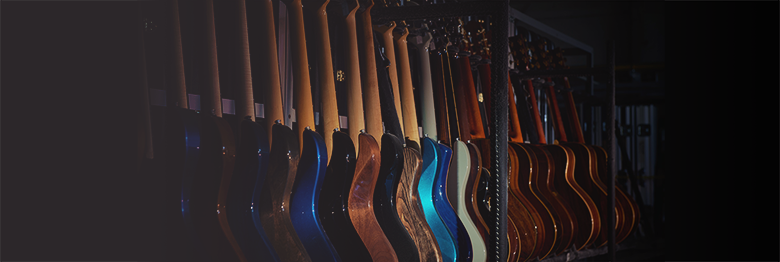
At Yamaha, the process of making great guitars begins long before the raw materials are delivered to the factory. Selection and procurement of woods and other materials are critical steps, but the Yamaha difference goes even further. The resources and facilities that Yamaha applies to basic research and development alone are more extensive than many guitar makers apply to actual production. And that level of involvement stretches back for decades, giving the company a stockpile of experience and know-how that makes it possible to deliver innovative features and refinements that make a real difference to guitarists. Traditional craftsmanship is still the mainstay of our guitar manufacturing, but innovative research and material optimization drives that craft forward.
THERE’S WOOD, AND THERE’S Yamaha WOOD
Ensuring that the woods used to build a great guitar deliver optimum performance requires special handling and crafting techniques that verge on the mystical, but as a global guitar maker, it’s essential for Yamaha to understand why the materials respond and perform how they do in order to deliver consistently high quality in every instrument. Yamaha’s extensive and vigorous materials R&D program not only provides the data needed to make the most of the woods available, but also makes it possible to modify and control their characteristics in ways that make them even more suitable for use in musical instruments, all to build better guitars.
DRYING TECHNOLOGY
Yamaha’s knowledge of wood drying comes from decades of experience in preparing woods for pianos, drums, bowed string instruments, woodwind instruments, marimbas, and more.After more than 50 years of leadership in the field, Yamaha continues to research and document drying methods, applying refinements as they become available to ensure consistently superior stability and performance in every instrument produced.
DRYING AND SEASONING
In Yamaha terminology, drying and seasoning are related but distinct processes that have different goals. Drying is initially employed to reduce the moisture content of the wood to a predetermined level, and seasoning then stabilizes the wood so that it maintains its dimensional and tonal characteristics through varying ambient conditions. Yamaha dries and seasons all of our own wood to ensure the best possible start for the instruments we build.
FINISHES AND ADHESIVES
Most of the finishes used on Yamaha guitars are formulated in-house. Off-the-shelf products don’t make the grade because, in addition to looking good and providing durable protection under a wide range of conditions, guitar finishes have to complement the instrument’s sound. Yamaha’s research centre develops the finish itself along with the application methods so every single guitar looks and sounds just right.
EXPERIENCE MAKES THE DATA MEANINGFUL
Since initial testing on individual components such as woods, finishes, or adhesives only reveals the characteristics of the materials themselves, a great deal of experience is required to be able to predict how those components will affect the overall performance of an instrument. Yamaha’s extensive history is the critical “secret ingredient” that throws light on the results, enabling engineers and craftsmen to apply them in meaningful ways.
WOOD REFORMING TECHNOLOGY ACOUSTIC RESONANCE ENHANCEMENT (A.R.E.)
It’s simple – old wood sounds better than new wood, especially on acoustic instruments. Through years of research, Yamaha’s R&D team found not only why aged woods sound the way they do, but also developed a process to replicate that ageing at a cellular level in the wood used to build new instruments. Using a proprietary combination of heat, moisture and pressure applied for a precisely determined time, Yamaha are able to make new guitars where the wood has the same properties, and the same sound, as perfectly aged vintage instruments.
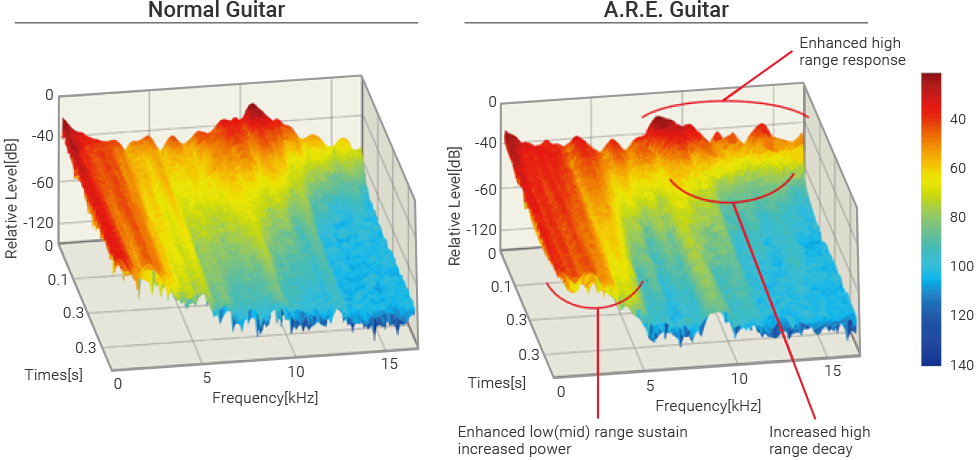
I.R.A. (INITIAL RESPONSE ACCELERATION)
Any guitar benefits from being "played in," a process in which the instrument matures and opens up as the stresses between the wood and finish, neck and fingerboard, and body and hardware are released, resulting in better sound and playability.
Yamaha’s exclusive Initial Response Acceleration (IRA) technology releases those stresses by applying specific vibrations to the completed instruments as part of the crafting process and gives a "played in" guitar from day one.
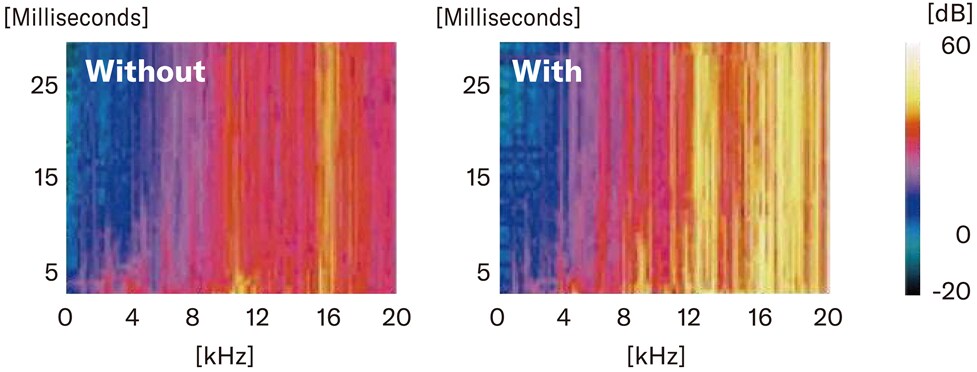
РАЗРАБОТКИ И ИССЛЕДОВАНИЯ
МАСТЕРСТВО ИЗГОТОВЛЕНИЯ
КОНТРОЛЬ КАЧЕСТВА
АКУСТИЧЕСКИЙ АНАЛИЗ
УСТРОЙСТВО АКУСТИЧЕСКОЙ ГИТАРЫ
УСТРОЙСТВО ЭЛЕКТРОГИТАРЫ
ОБСЛУЖИВАНИЕ: ЗАМЕНА СТРУН