Quality control
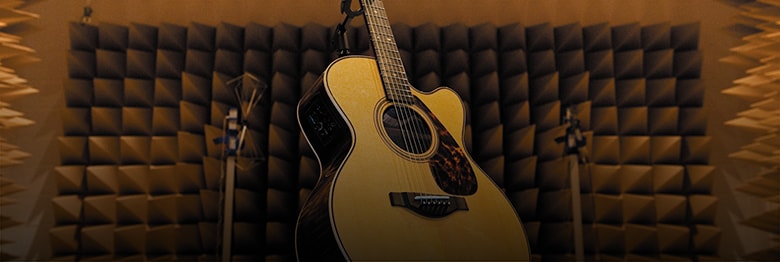
At Yamaha, quality control means way more than simply checking finished products for defects. Everything from how a guitar copes in extremes of hot and cold, to how the strap pins hold up when a guitar is dropped is thoroughly and systematically checked from the first moment a new guitar is envisioned, to make sure that the guitar in your hands can handle everything you throw at it, day after day, night after night.
Creating Quality that Lasts
1: Virtual Review – Creating Quality on Paper
The Yamaha approach is to build quality into every guitar right from the beginning. This means that a proposed design will be subjected to multiple virtual review sessions while the instrument is just an idea on paper.
Every aspect of the proposed guitar, including the tools and methods for how it will be constructed, is thoroughly reviewed by designers, engineers, luthiers and players from inside and outside of Yamaha. Only when everyone involved is satisfied does development proceed to the next step.2
2: Initial Prototype – Ideas Become Reality
Phase two of the development process is the construction of the first prototype. Built according to the specifications that come out of phase one, the first prototype is once again subjected to multiple reviews. New features, in particular, are examined in detail to determine whether they actually fulfil a need and whether there’s any way they might be improved.
3: Pre-production Prototype – Refining the Process
Once the first prototype gets the green light from the review teams, a second “pre-production” prototype is made. The second prototype is used both to check for issues that may have arisen since the last review, and to refine the production process by which the instrument will be made. Every design requires its own special manufacturing techniques, so every tool, jig, and process that will be used to build the final instrument is reviewed in detail.
4: Production – Non-stop Quality Control
Making a Yamaha guitar involves skilled craftspeople at every step. This level of hands-on attention means that each person who is drilling a hole, gluing bracing, shaping a neck, or applying a finish is monitoring the quality of the instrument as they work. Quality monitoring in Yamaha’s workshops is a continuous, uninterrupted process done with pride by the people making the guitars.
5: Spot Checks and Feedback from the Field – Continued Vigilance
Spot checks are regularly performed prior to guitars leaving the factory. If a problem is found on an instrument in production, shipment is stopped immediately and the cause is tracked down and rectified before shipment can resume.
Any problems reported by dealers or customers are treated similarly – thanks to Yamaha guitars being made in Yamaha factories, the communication chain to someone actually building the guitars is very short, meaning feedback can be acted on quickly and efficiently. Yamaha’s QC department even buys guitars from music stores to perform random, independent, real-world testing.
6: In the Player’s Hands – Lasting Quality
A good guitar should last a lifetime, but a guitar that gets played will wear over time and need ongoing maintenance to keep it in optimum condition. Yamaha maintains stocks of parts that might be needed to repair and service guitars for up to 10 years after the product has been discontinued, sometimes longer.
Severe Quality Testing
Since quality cannot be fully assured on the basis of theory alone, it’s necessary to subject actual instruments and parts to controlled abuse in order to test their actual performance, stability, and resilience to extremes. Yamaha maintains a number of facilities dedicated to physical testing and quality control – including the world-class Yamaha Quality Support Center that houses some of the most advanced and sensitive testing facilities for electronic devices available anywhere, plus some tortuous durability tests that push instruments far beyond the limits of normal use.
Accelerated Environmental Testing
A well made guitar has to withstand a range of environmental conditions without damage or compromised playability; a neck that warps with every change in humidity is close to useless. At the extremes wood can crack and glue joints can separate - none of these things are acceptable for Yamaha guitars.
To ensure that Yamaha guitars remain stable and reliable in all conditions, year after year, instruments are subjected to accelerated testing that simulates the severest conditions imaginable. The test instruments are be kept at -20 degrees Celsius and then moved to a +50 degree environment, repeated several times while measurements are made to check integrity and stability. The same process is used for extremes of atmospheric moisture, with instruments being subjected to alternating periods at 90% and then 20% humidity.
Vibration and Drop Testing
Guitars need to be shipped around the world, from the factory to local distribution centres, to dealers and finally into players hands – arriving at each step playing, looking and sounding great. Ships, trucks, planes and couriers are notoriously hard on guitars, so packaging and shock resistance are crucial quality issues. Yamaha’s testing is brutally simple: drop the guitar from a significant height onto its corners as well as top, bottom, and sides, and subject it to severe mechanical vibration covering a range of frequencies for extended periods. If the guitar and packaging can survive this, they can survive transportation around the globe under even the roughest conditions.
The Ultimate Goal
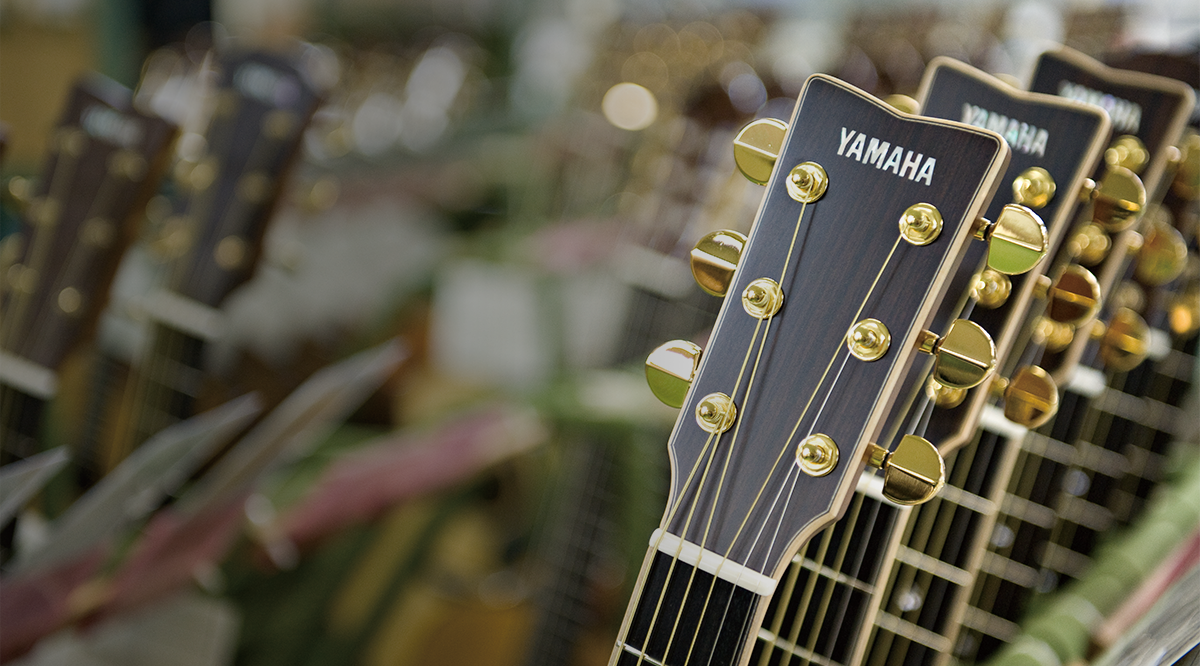
The ultimate goal of Yamaha quality control is to make guitars that fulfil a player’s musical needs and are capable of growing and improving along with the player for many, many years.
Like the guitars themselves, Yamaha’s quality management systems continually evolve to keep pace with continuously changing markets, user needs, and technology. Checking, changing and continuously monitoring at every stage takes a massive effort, but keeps us ahead of the game and keeps our guitars performing every time they’re picked up, year after year.
РАЗРАБОТКИ И ИССЛЕДОВАНИЯ
МАСТЕРСТВО ИЗГОТОВЛЕНИЯ
КОНТРОЛЬ КАЧЕСТВА
АКУСТИЧЕСКИЙ АНАЛИЗ
УСТРОЙСТВО АКУСТИЧЕСКОЙ ГИТАРЫ
УСТРОЙСТВО ЭЛЕКТРОГИТАРЫ
ОБСЛУЖИВАНИЕ: ЗАМЕНА СТРУН